Top 10 Tips for Effective Construction Quality Control in 2024
Introduction
Quality control (QC) is the backbone of successful construction projects. In 2024, as the construction industry continues to evolve with new technologies, materials, and methodologies, ensuring high-quality work is more crucial than ever. Quality control is not just about meeting the bare minimum standards but about exceeding expectations to deliver durable, safe, and sustainable structures. Whether you’re a contractor, project manager, or construction worker, understanding the intricacies of construction quality control will set your projects apart in a competitive market.
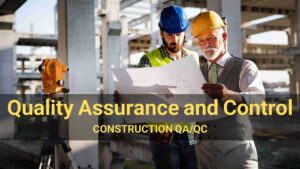
This comprehensive guide will explore the top 10 tips for effective construction quality control in 2024. From embracing cutting-edge technologies to refining your on-site practices, these strategies will help you ensure that your projects meet and exceed industry standards.
1. Implement Advanced Quality Management Systems (QMS)
As construction projects grow in complexity, traditional quality control methods may no longer suffice. Investing in an advanced Quality Management System (QMS) can streamline the quality assurance process. These systems are designed to manage all aspects of construction quality, from design to completion, by automating tasks, tracking progress, and ensuring compliance with industry standards.
Key Benefits:
- Centralized Data Management: A QMS integrates all quality-related data into a single platform, making it easier to track and manage.
- Real-time Monitoring: Automated systems allow for real-time monitoring of quality metrics, reducing the chances of errors.
- Compliance Assurance: QMS ensures that all processes comply with local, national, and international standards, reducing the risk of costly rework.
2. Prioritize Training and Certification
A well-trained workforce is essential for maintaining high-quality standards on construction sites. Investing in continuous training and certification programs ensures that your team is up-to-date with the latest industry practices, technologies, and safety protocols.
Training Focus Areas:
- New Technologies: As construction tools and materials evolve, so should your team’s knowledge and skills.
- Safety Protocols: Regular safety training reduces the likelihood of accidents, which can compromise quality.
- Quality Standards: Familiarize your team with industry-specific quality standards and how to achieve them consistently.
3. Leverage Construction Technology and Automation
The integration of technology in construction has revolutionized quality control processes. From drones to AI-powered inspection tools, technology can help you identify potential issues before they become costly problems.
Technologies to Consider:
- Drones: Use drones for aerial inspections of large construction sites. They provide a bird’s eye view, helping to identify inconsistencies that might not be visible from the ground.
- AI and Machine Learning: AI-powered tools can predict potential quality issues by analyzing historical data and current project metrics.
- Building Information Modeling (BIM): BIM helps in visualizing the project in 3D, allowing for better planning and detection of design flaws early in the construction process.
4. Adopt Lean Construction Practices
Lean construction focuses on minimizing waste and maximizing value throughout the project lifecycle. By adopting lean practices, you can improve efficiency, reduce costs, and enhance the overall quality of the project.
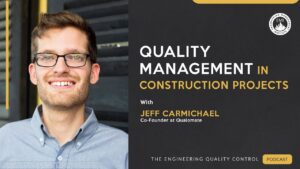
Lean Principles to Implement:
- Value Stream Mapping: Identify and eliminate processes that do not add value to the project.
- Just-in-Time Delivery: Reduce material waste and storage issues by ensuring that materials arrive just when they are needed.
- Continuous Improvement: Encourage a culture of continuous improvement where every team member is responsible for suggesting and implementing quality improvements.
5. Conduct Regular Site Inspections and Audits
Regular site inspections and audits are critical for maintaining quality control. These inspections should be thorough, covering all aspects of the construction process, from foundation work to finishing touches.
Inspection Best Practices:
- Checklists: Develop detailed checklists for each stage of construction to ensure that nothing is overlooked.
- Third-Party Audits: Consider hiring third-party inspectors to provide an unbiased assessment of your project’s quality.
- Documentation: Keep detailed records of all inspections and audits, including photos and notes, to track progress and address issues promptly.
6. Use High-Quality Materials and Suppliers
The quality of materials used in construction directly impacts the longevity and safety of the structure. Partnering with reputable suppliers and insisting on high-quality materials is non-negotiable for achieving superior construction outcomes.
Tips for Material Selection:
- Supplier Vetting: Conduct thorough vetting of suppliers to ensure they meet your quality standards.
- Material Testing: Regularly test materials to verify their quality before use on site.
- Sustainability: Consider using sustainable materials that not only meet quality standards but also contribute to environmental conservation.
7. Integrate Quality Control into Project Planning
Quality control should not be an afterthought but an integral part of project planning. By incorporating quality measures into the planning phase, you can identify potential issues early and develop strategies to mitigate them.
Planning Strategies:
- Set Quality Benchmarks: Establish clear quality benchmarks that align with industry standards and client expectations.
- Risk Management: Identify potential quality risks during the planning phase and develop contingency plans.
- Stakeholder Involvement: Involve all stakeholders, including clients, contractors, and suppliers, in the quality planning process to ensure everyone is on the same page.
8. Utilize Data Analytics for Quality Control
Data analytics can provide valuable insights into your construction processes, helping you identify patterns and trends that may affect quality. By analyzing data from past projects, you can make informed decisions that enhance future project outcomes.
How to Use Data Analytics:
- Performance Metrics: Track key performance indicators (KPIs) related to quality, such as defect rates, rework costs, and inspection outcomes.
- Predictive Analysis: Use predictive analytics to foresee potential quality issues and address them before they escalate.
- Continuous Monitoring: Implement systems for continuous monitoring of quality metrics throughout the project lifecycle.
9. Foster a Quality-Centric Culture
A strong quality culture within your organization ensures that every team member is committed to maintaining high standards. This involves setting clear expectations, providing ongoing training, and recognizing efforts to uphold quality.
Building a Quality Culture:
- Leadership Commitment: Leaders should demonstrate a commitment to quality, setting an example for the rest of the team.
- Employee Empowerment: Empower employees to take ownership of quality by encouraging them to speak up about potential issues and suggest improvements.
- Recognition Programs: Implement recognition programs that reward team members for their contributions to maintaining or improving quality standards.
10. Emphasize Communication and Collaboration
Effective communication and collaboration among all stakeholders are essential for maintaining quality control. Clear communication ensures that everyone understands the quality expectations and their role in achieving them.
Communication Strategies:
- Regular Meetings: Hold regular meetings with all stakeholders to discuss quality goals, progress, and challenges.
- Transparent Reporting: Ensure that quality metrics and inspection results are transparently shared with all relevant parties.
- Collaborative Tools: Use collaborative tools like project management software to keep everyone aligned and informed.
Conclusion
In 2024, construction quality control is more than just a requirement; it’s a competitive advantage. By implementing the top 10 tips outlined in this guide, you can ensure that your projects not only meet but exceed quality standards. From adopting advanced quality management systems to fostering a quality-centric culture, each of these strategies plays a crucial role in delivering high-quality construction projects that stand the test of time.
Investing in quality control is investing in the future of your construction business. By prioritizing quality at every stage of your projects, you’ll build a reputation for excellence that attracts more clients, reduces rework costs, and ultimately, increases profitability.
Start implementing these tips today and set your construction projects on the path to success in 2024 and beyond.
If you want to get more knowledge about this so read more.
If you want more articles about Civil Engineering click on link.